Lifelong learning benefits you as a person, therefore we support the growth of our employees with all our heart. Toyota Material Handling Europe has developed online tools for its employees to expand their knowledge and skills, like our TMHE academy. These tools are supported by complete training programmes, like our Service Technician Education Programme or STEP. We asked Antoine Reminiac (Senior Operations Development Manager for Service Market) what STEP is all about.
At Toyota Material Handling we have a STEP-training for technicians, what is that exactly?
‘Well, STEP is a training development programme that exceeds the technical fundamentals of the technician’s job. They’ll learn about our company culture, tools, safety, customer interaction and so on. They’ll get a thorough understanding of everything that is required within their job as technicians
There are three levels in our STEP-training: Bronze, Silver and Gold.’
‘The Bronze level covers the basics; technicians join Toyota Material Handling, they learn about our company and its values. During their first weeks we provide them with the basics: customer interaction and truck knowledge, safety guidelines, information about how to find support etcetera. They also get to work with tools like T-Stream. We call this step “onboarding and product knowledge”.’
‘After a few years of field experience, a technician can deepen his or her technical expertise by taking our Silver STEP; this part of the programme focusses on strengthening technical knowledge and efficiency. This way they become experts on any type of product. Eventually, some will have the opportunity to become “senior technicians”; these technicians specialise in dealing with challenging customers, like those who need immediate repairs, or have a set of complicated equipment, or customers with autonomous vehicles.'
‘Through Gold STEP, employees get a grasp of how to grow in our company by studying various soft skills such as time management, communication, and leadership to potentially become Service Leaders or managers.’
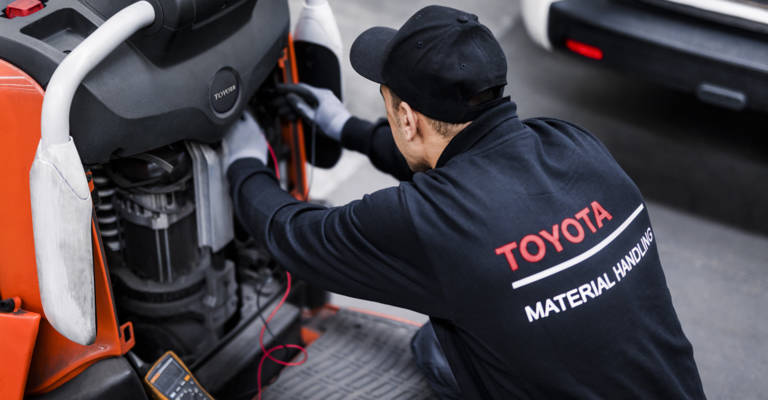
What does one of these typical training days look like?
‘Traditionally, training sessions take place in a classroom or workshop. We also added a digital orientation. We try to mix online classes with physical ones as not everything can be taught online. Technicians get the theory online, they then put it into practise by spending time working on the truck with their trainer, by service roleplay or even by joining our digital classroom, where the trainee takes control of the trainer’s laptop to configure the truck, while the trainer can correct him or her.’
‘We design the training centrally, then present it to our national trainers in every country. They decide when the training will take place. When a new product is launched, a couple of days of training help the technicians understand what’s new compared to the product’s previous generation.
How do you evaluate technicians?
‘We use an online quiz to test their theoretical knowledge. To test their practical skills, we give them exercises in the workshop. In the future, we will ask their team leaders to assess their competence in the field, as we want to be more competence than knowledge focussed in our approach. After all, the most important thing is that they put their knowledge from the training into practise during fieldwork.’
Can technicians apply for extra training?
‘Yes, of course. Every year our technicians have the chance to sit down with their managers and make up a plan. It’s the responsibility of our local service team and of HR to make sure our technicians receive qualitative training.’
How do you motivate technicians to develop their skills?
‘We try to make our courses as attractive as possible; we put our training development programme in the spotlight, to recruit candidates. We notice that offering tools and platforms to develop their competences is an important source of motivation for our trainees; they want to become really good at their job and be able to professionally represent our brand when facing customers.’
‘We also organise a European skills contest where we put technicians from several countries to the test, the winners get to go to Japan. It’s a low-pressure contest and a fun team activity. It’s also a communication platform amongst technicians and a way for us to see which topic needs extra attention, if many technicians fail on a certain topic, we have to train them more on said topic. This coincides with our values of “Genchi Genbutsu” (going to the source) and “Kaizen” (continuously striving to get better).’
What do you think the future will bring for these trainings?
‘Digital tools will play an important role. We have a new blended approach: digitalisation should support human relations but shouldn't replace them. Recently, we started using a 360° video tool that immerses our trainees into a real work environment. Our trainees can become even more engaged via a VR-set. We also pay attention to our experienced technician: we try to continuously develop new and enticing content to make sure that they keep evolving throughout their careers.’
‘Onboarding will also be key, as recruiting people and spreading company culture is more complex in a digital era. Our scope is wider and there are many tools that our technicians have to use. However, we aim to provide our technicians with qualitative training.’
At Toyota, we believe that a balanced education is the key to success, even in pandemic times. Not only our technicians, but all of our employees are offered courses, classes, or workshops to stimulate their critical thinking and practical skills. We make our education programmes captivating and challenging so our employees keep growing throughout their career.